Understanding Glove boxes: A Comprehensive Overview
In the intricate landscape of laboratory work, where safety is paramount, few tools are as indispensable as glove boxes. They offer researchers the ability to handle delicate materials or shield against hazardous substances. With a multitude of applications spanning various industries, it’s crucial to understand the different types of glove boxes and their distinct capabilities to choose the right fit for your specific application. Selecting the right glove box type can transform your workflow, providing safety and enhancing efficiency.
Defining Efficiency and Safety
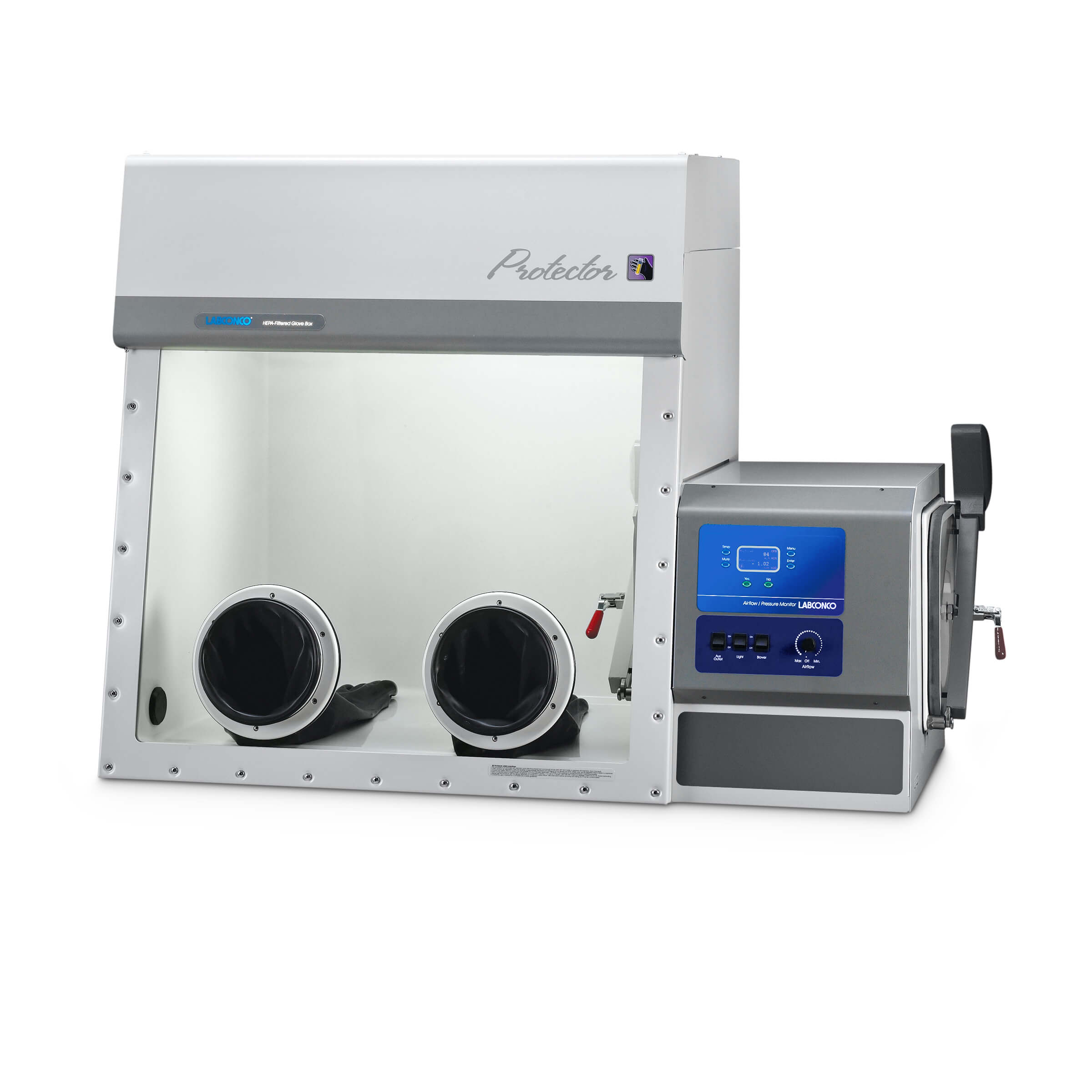
Glove boxes, such as moisture isolators or barrier isolators, are designed to prevent protect the researcher (HEPA filtered glove boxes) and sensitive materials (controlled atmosphere glove boxes). Equipped with high-efficiency particulate air (HEPA) or ultra-low penetration air (ULPA) filtration, these glove boxes create an ISO Class 1 barrier to safeguard against external factors or to contain internal hazards. These filters are capable of trapping minute particles, making them suitable for tasks demanding strict hazard control.
Ideal Applications:
-
Pharmaceutical Research: Handling and testing of potent compounds, active pharmaceutical ingredients (APIs), and drug formulation under sterile conditions.
-
Nanotechnology: Manipulation and assembly of nanoparticles in a safe environment.
Crucial Considerations:
-
Inlet and Exhaust Filtration: It is critical to determine whether both incoming and outgoing air necessitate particulate filtration. When shielding the contents inside the chamber from environmental particles, inlet filtration becomes essential. If the materials within the chamber contain hazardous particles, then the exhaust airflows must undergo filtration.
-
HEPA or ULPA Filters: HEPA filters provide 99.9% filtration of particles smaller than 0.3 μm. ULPA filters excel in capturing nano-particulates.
-
Exhaust Ventilation: If exhaust contains harmful fumes or gases, venting outside is imperative, as particulate filters are ineffective against such contaminants.
-
Internal Pressure Management: It’s important to balance the internal pressure within the glove box. Negative pressure ensures hazardous particulates remain contained.
Controlled Atmosphere Glove boxes: Inert Gas Environments
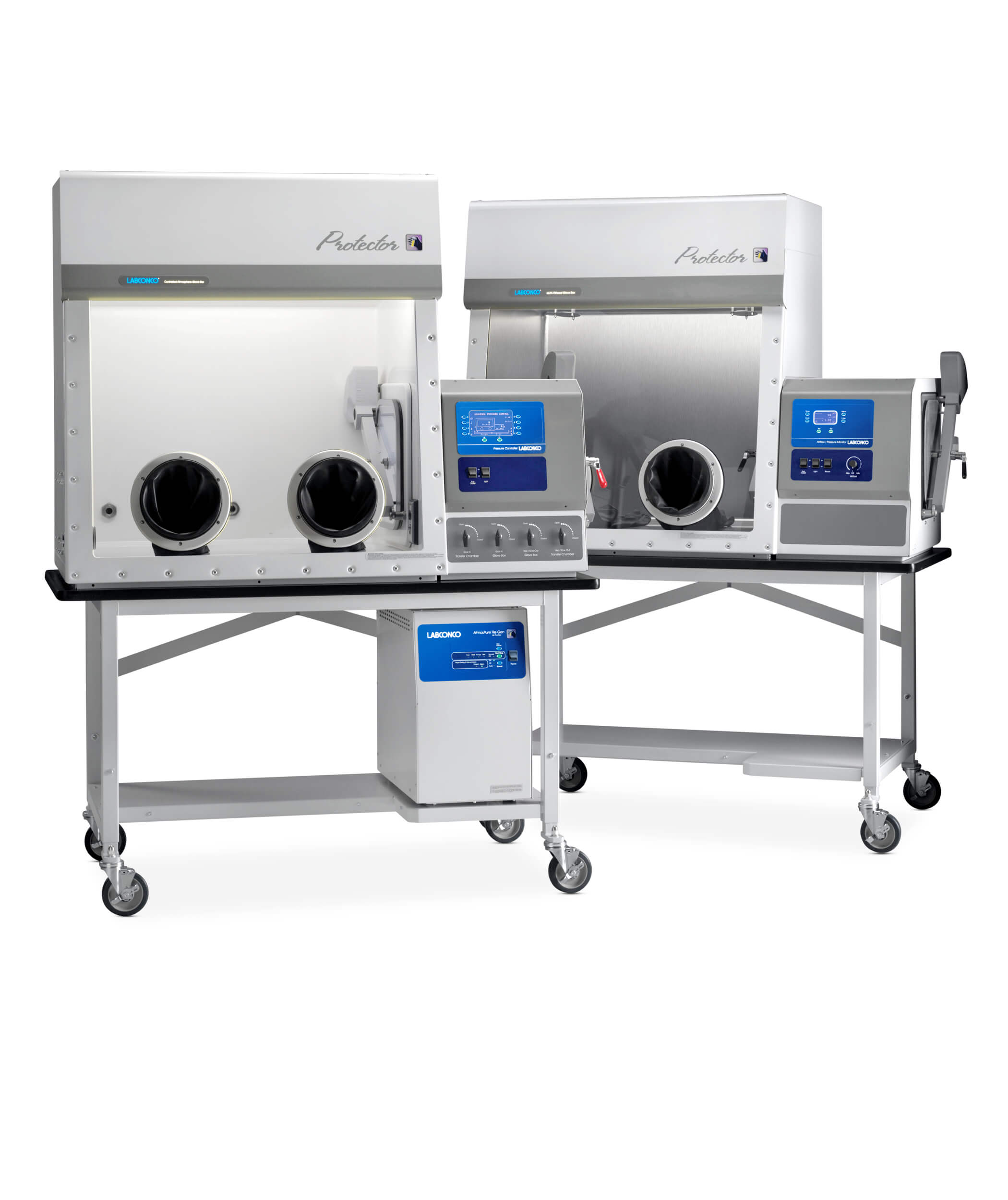
Controlled atmosphere glove boxes, also known as inert gas glove boxes or dry boxes, maintain a leak-tight controlled environment for sensitive materials. These glove boxes function as controlled chambers, allowing researchers to manipulate the level of oxygen, moisture and/or other gases. They utilize a series of valves connected to purified, compressed inert gas sources to create specialized environments tailored to specific applications.
Ideal Applications:
-
Material Science: Synthesis and handling of oxygen-and-moisture-sensitive compounds, metal organic frameworks (MOFs), and catalyst research.
-
Electrochemistry: Development and testing of batteries, fuel cells, and energy storage systems in controlled gas environments.
-
Environmental Studies: Analysis of gas interactions, corrosion or oxidation.
Crucial Considerations:
-
Atmosphere Control: A controlled atmosphere glove box creates an application specific inert gas environment.
-
Purification Methods: Constant flush or purge and fill methods ensure chamber purification.
-
Choice of Purified Gas: Nitrogen and argon are common inert gases.
-
Enhanced Purification: Advanced systems combine purge and fill with recirculating oxygen and moisture removal to achieve ultra-low concentration levels.
-
Application Variability: Oxygen and moisture levels vary based on applications, from ≤1 ppm to 10,000 ppm or higher.
The search for the right glove box involves consideration of numerous factors. Defining application goals and adhering to specific requirements ensures optimal glove box selection, simplifying the process and conserving both time and resources.