What's in a name? Not much, in the glove box world
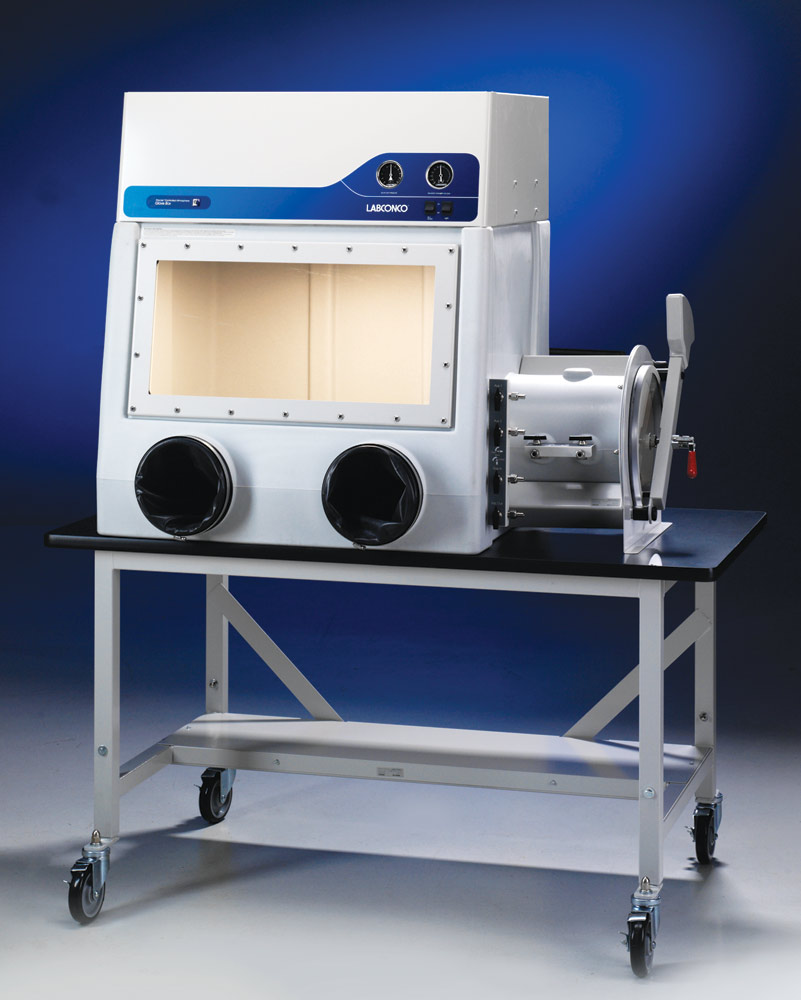
Over the last two decades in the United States, there has been an increase in the use of glove boxes for a growing number of applications. Scientists, engineers, manufacturers and facilitymanagers have started using new terms for these devices in an effort to better define and categorize specific glove box applications. The terms isolator, isolator glove box, glove box isolator, and barrier isolator are now commonly used to describe a glove box and its functions. Unfortunately, expedient terminology usually falls short of defining the operational requirements for any specific glove box.
In general terms, there are two types of glove boxes: they include isolator glove boxes that are filtered by ventilation and controlled atmosphere glove boxes.
Isolator Glove Boxes
The term isolator most often implies the use of HEPA (High Efficiency Particulate Air) or ULPA (Ultra Low Penetration Air) filtration for a glove box application. Isolation can mean keeping something out or keeping something in. Is that ‘something’ hazardous to humans, or are humans hazardous to the ‘something’? What is the application goal? Answers to these questions, as well as those that follow, will help determine the precise glove box needed.
Will both inlet and exhaust air streams require particulate filtration?
For many applications, the materials inside the box need to be protected from common environmental particulates. So, inlet filtration is required. If those materials generate hazardous particulates, exhaust airflows must also be filtered.
Should HEPA or ULPA filters be used?
Both HEPA and ULPA filters provide ISO Class 5 sterile air. ULPA filters provide a better capture profile if nanoparticulates are a concern.
Will the exhaust air need to be vented to the outside?
If the exhaust contains harmful fumes or gases, exhausting to the outside is required. Particulate filters do not trap these contaminants.
Should the internal glove box pressure be positive, negative or adjustable?
Hazardous particulates inside a glove box should be kept under negative pressure. Maintaining a sterile environment inside a glove box might require positive pressure. What can be done, then, if the material inside needs to be kept sterile and is hazardous? To help answer this question, leak tightness should be reviewed. ISO (the International Organization for Standardization) 10648-21¹ classifies containment enclosures based on their leak tightness and provides methods for checking a glove box’s leak rate. Many glove boxes are extremely leak tight, and safety concerns regarding positive/negative pressure operations often become a non-issue.
Should the filtered airflow maintain an internal sterile air volume condition?
Air volume sterility is not the same as surface sterility, which will be addressed later. Diluting the internal air volume with sterile air can ultimately produce a sterile air volume, but this does not mean the surfaces inside the glove box are sterile.
Will the air volume and the internal glove box itself need to be entirely sterile?
In order to maintain a total sterile environment, the airflow within a glove box should be laminar. The glove box must also be connected to a Vaporous Hydrogen Peroxide (VHP) system. The VHP system, when used correctly, can ensure surface sterility within the glove box before operations begin. Glove boxes for this application can be quite complicated and costly.
Is sterility the correct condition, or is a decontaminated environment the real operational goal?
The answer to this question can be found in many different private and governmental organizational standards such as those provided by the FDA, USP, CETA, etc.
As this review of product application questions indicates, searching for an isolator is an involved process. Many factors must be taken into consideration before a glove box for a specific application can be selected.
Controlled Atmosphere Glove Boxes
Controlled atmosphere glove boxes also have many not-so-descriptive names: these include dry boxes, inert boxes, nitrogen boxes, low oxygen and/or moisture boxes, hypoxia boxes and anaerobic boxes.
All of these glove boxes have one thing in common: they are generally leak-tight enough to provide some level of control over the internal gas atmosphere using a series of valves connected to a purified compressed gas source. The specific contaminant ranges and the required operation gases are the two most important details that must be communicated in any controlled atmosphere glove box discussion.
In order for a controlled atmosphere glove box to function, the internal ambient atmosphere gas contaminants must be removed and replaced with an alternative or purified gas. There are two methods of internal chamber purification. In a constant flush system, a continual flow of inert gas is required. In a glove box that utilizes an evacuation/refill method, positive pressure gas and a negative pressure vacuum allows the main chamber of the glove box to be evacuated and subsequently refilled with the inert gas. The appropriate purified gas depends on the application, but the most common gases are the inert gases, such as nitrogen and argon. In some applications, such as those performed in hypoxia or anaerobic glove boxes, standardized gas mixtures are required.
For some controlled atmosphere glove boxes, the only contaminant removal system used is the gas evacuation and refill operation. Oxygen and moisture levels are reduced to 1-10%, and operations are completed within a normal eight-hour day. Other, more sophisticated controlled atmosphere glove boxes utilize a recirculating oxygen and/or moisture removal system along with the initial evacuation and refill operation to achieve and maintain extremely low (≤1 ppm) concentration levels. These accessory systems, which can be recharged when the oxygen/moisture removal catalysts become expended, are required to compensate for constant contaminant permeation occurring through the gloves regardless of the glove box internal pressures.
While some controlled atmosphere glove boxes create inert gas atmospheres with oxygen and moisture contamination levels maintained at ≤ 1 ppm, other applications, such as those performed in hypoxia glove boxes, require oxygen levels of 200 ppm or higher. Still other applications, such as long-term product stability assays, require oxygen and/or moisture levels to reach 1% (10,000 ppm) or higher.
Conclusion
Simplistic labels are not enough to convey the entire scope of operation and design requirements for a glove box system. No matter what you call your glove box, be prepared to specifically define your application goals and requirements. Matching a glove box to a well-defined application is easy. Working with guesses and looking for a single glove box to cover all possible outcomes is costly and results in wasted time and money.
____________________________
References
¹ISO 10648-2:1994. Geneva: ANSI,1994. Print.